Msc: Sustainable Engineering : Chemical and Process Engineering
Challenges of Cow Manure
While cow manure can act as a steady supply of feed for an anaerobic digestion process, it comes with two major challenges for maximising biogas production: Its core components, and its carbon to nitrogen ratio. In the solid quantities of the cow manure, there is a significant amount of lignocellulosic material which comprises 40-50% of the dry weight of the cow manure (Kims et al., 2023). This material is comprised of cellulose, hemicellulose, and lignin. The latter two components, inhibit the production of methane by ensnaring cellulose and reducing the access sites for cellulose to react, seen in figure 1.

Figure 1: Lignocellulose: a complex compound that hinders AD. (Jung et al., 2022)
There are several pre-treatment methods available to increase methane production from the dairy manure. These include mechanical, thermal and chemical pre-treatment
Pre-Treatment Methods
Ultimately, it was decided to use a thermal hydrolysis system as it is capable of generating a greater methane yield while also trying to keep costs low for the overall system. This form of treatment also has the advantages of being easier to control compared to chemical treatment. By applying high temperatures to the feed, we can reduce the amount of hemicellulose that is present in the feed and allow cellulose molecules better access to water and promote increase conversion. There is a risk however of generating refractory compounds such as furfural and xylose which can inhibit biogas production. (Kim, Lee, & Kim, 2023b)
1
Mechanical
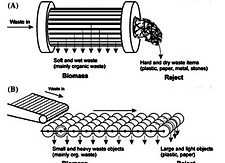
Figure 2: Mechanical treatment (Das et al., 2015)
Mechanical treatment involves using machinery to mash, pulp or shred the manure, which reduces the particle size of the lignocellulose sites. Doing this allows the microbes involved in the AD process better access to cellulose for biogas production. The process however is energy intensive and and the methane yield increase is not as great as other pre-treatment methods.
2
Thermal
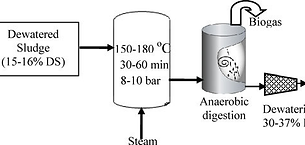
Figure 3:Thermal treatment (Pilli et al., 2014)
Thermal treatment involves heating the manure at high temperatures and pressures in order to break up the hemicellulose lattice and open up access to cellulose, while also killing off pathogens in the manure which can be hazardous to health such as E.coli. Thermal treatment can also be energy intensive at temperatures above 180áµ’C, however it has greater methane yield than mechanical treatment even at temperatures below 180áµ’C. (Nadan & Baroutian, 2023)
3
Chemical

Figure 4: Chemical treatment (Bharadwaj et al., 2023)
Chemical treatment utilises acids or alkalis to break down the lignocellulose. When acids are used there is a breakdown in the Van Der Waal forces holding the structure together. When bases are used, there is a breakdown in lignin and in the structural order in the compound. This treatment has the highest methane yield but has high costs for acids/alkalis and the environment of the reaction has to be tightly controlled so conditions remain optimal. (Nguyá»…n et al., 2021)

Another issue with dairy manure is that it contains a low carbon to nitrogen ratio. The optimum C:N ratio is between 20:1 and 30:1. For cow manure, the typical C:N ratio is15:1. In order to boost this ratio, it is possible to combine the manure feed with another substrate of higher C:N ratio to create a combined ratio that is in the optimum range. This is known as anaerobic co-digestion. One choice to improve this ratio is dry distillery grains with solubles (DDGS) these are the waste by-products from distillery business and contain a carbon nitrogen ratio between 37:1 - 42:1.(Sensai et al., 2014)
Figure 5: Distillery Dried Grains with Solubles (DDGS)
By combining this feed with the cow manure we can get a carbon nitrogen ratio between 26:1 - 29:1. It has been shown that increasing the amount of DDGS can linearly increase the methane yield in the system (Akamine et al., 2023). DDGS from barley was selected due to its high availability in Scotland, with an annual production of just over 200,000 tonnes of distillery grains (The Scottish Government., 2019). From the proposed design, only 1% of this annual production would be used (approximately 2,000 tonnes). Additionally, DDGS is an easy substance to store and does not spoil for several years. This means that the system can have a constant supply of feed, even when the Scottish distilleries close during the summer and winter.

Figure 6: Annual production of DDGS from wheat and barley in Scotland